18 октября в селе Мячково Коломенского округа была запущена первая линия сортировочного цеха в комплексе обработки коммунальных отходов КПО «Юг». В течение месяца будут завершены пуско-наладочные работы, после чего комплекс заработает на полную мощность и сможет принимать до 650 тысяч тонн отходов в год.
Строительством занималась входящая в Госкорпорацию «Ростех» компания «РТ-Инвест» - самый крупный оператор раздельного сбора отходов на территории Московской области. Она контролирует три из семи кластеров региона: Сергиево-Посадский, Рузский и Каширский. Объем инвестиций в предприятие составил 3.5 млрд рублей, однако, по словам главы «Ростеха» Сергея Чемезова, планируется дальнейшее расширение комплекса и вложение еще 3 млрд рублей.
«Это позволит увеличить существующую мощность на 40% и в конечном счете прийти к нулевому захоронению отходов в этом округе», - заявил Чемезов на церемонии открытия комплекса.
Коломенский КПО построен в рамках нацпроекта «Экология» и является первым из четырех подобных комплексов, которые будут введены в эксплуатацию в Подмосковье в 2019-2020 годах. Два из них планируют запустить до конца этого года, еще один - в следующем. Recycle побывал на открытии и подробно изучил работу нового комплекса.

Раздельный сбор во дворах
В начале этого года на территории Московской области начала вводиться система раздельного сбора отходов у населения «Два бака». Синие контейнеры служат для сбора так называемых «чистых» фракций: макулатуры, стекла, металла и пластика, не загрязненных пищей.
Серые баки предназначены для органики и смешанного мусора: предметов гигиены, масляных емкостей, а также упаковки и посуды, загрязненной продуктами питания. Помимо баков предусмотрена площадка для сбора крупногабаритной техники и мебели.
В Подмосковье уже функционирует около 26 тысяч таких контейнерных площадок - каждая из них оцифрована. Для опорожнения баков приезжают две разные машины - одна собирает по городу содержимое чистых синих сеточек и крупногабаритные отходы, а другая предназначена для серых контейнеров. Водители мусоровозов фотографируют баки до и после выполнения своей работы. Эти данные передаются региональному оператору для сбора статистики и фиксации нарушений.
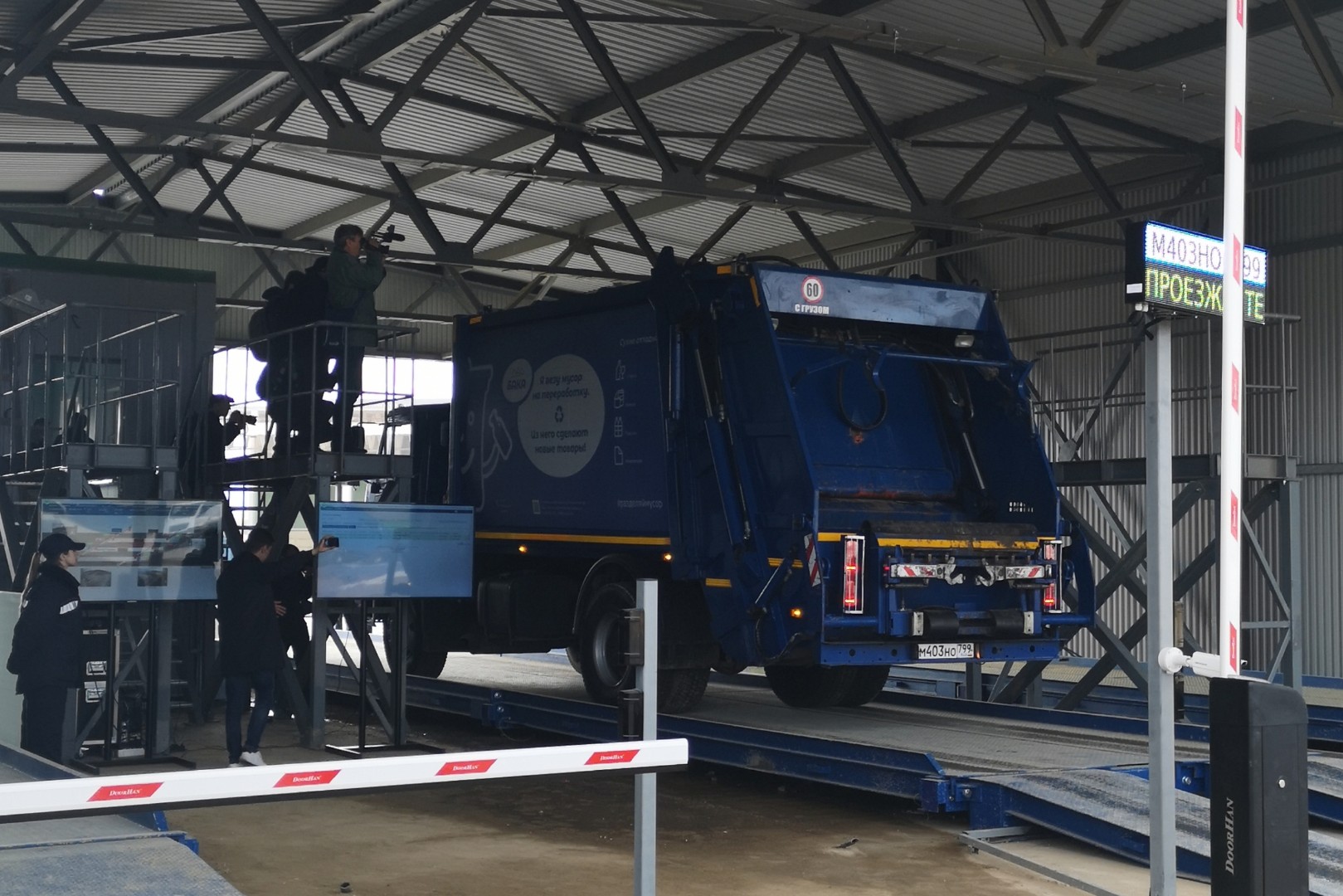
Взвешивание отходов
Дальше мусоровоз едет на ближайший комплекс переработки отходов. Прежде чем попасть на территорию комплекса, каждая машина проходит радиационный контроль и взвешивание. Этот процесс ведется в автоматическом режиме. Система сама распознает номер мусоровоза и проверяет наличие электронного талона, который водитель оформляет при въезде.
В базу уже внесены номера тех машин, которые участвуют в сборе и транспортировании отходов – это позволяет устранить завоз мусора с незаконных свалок. Как только положительный отклик из базы данных получен, шлагбаум поднимается, а машина заезжает на взвешивание.
На весах со специальными датчиками фиксируются масса и объем привезенных отходов, другое оборудование считывает радиационный фон, чтобы на сортировку не попали опасные отходы. После прохождения этой процедуры мусоровоз пускается на разгрузку. Особые весы и систему автоматического учета и контроля разработали отечественные специалисты из «ТКО-Информ». Все собираемые на этом этапе данные также передаются региональному оператору и открыты для проверяющих и надзорных органов.
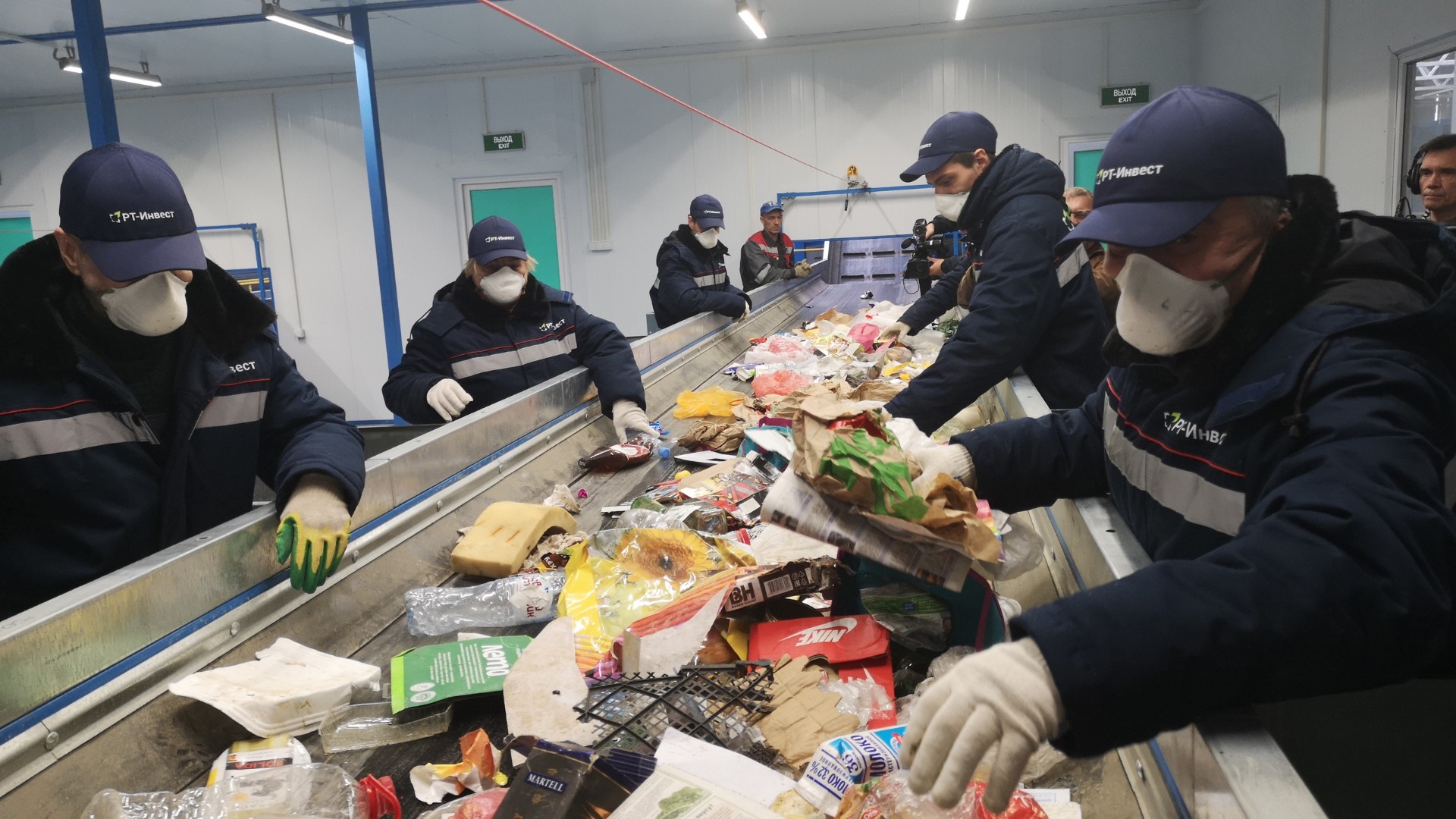
Сортировка на КПО
В Коломенском комплексе будут обрабатывать, перерабатывать и частично захоранивать некоторые типы отходов. Он станет крупнейшим из действующих в России комплексов с круглосуточным режимом работы. Обслуживать комплекс будут более 560 сотрудников.
«Обрабатывать» станут полезные фракции: бумагу, металл, стекло, пластик - все это упакуют в брикеты (кроме стекла) и отправят сторонним переработчикам.
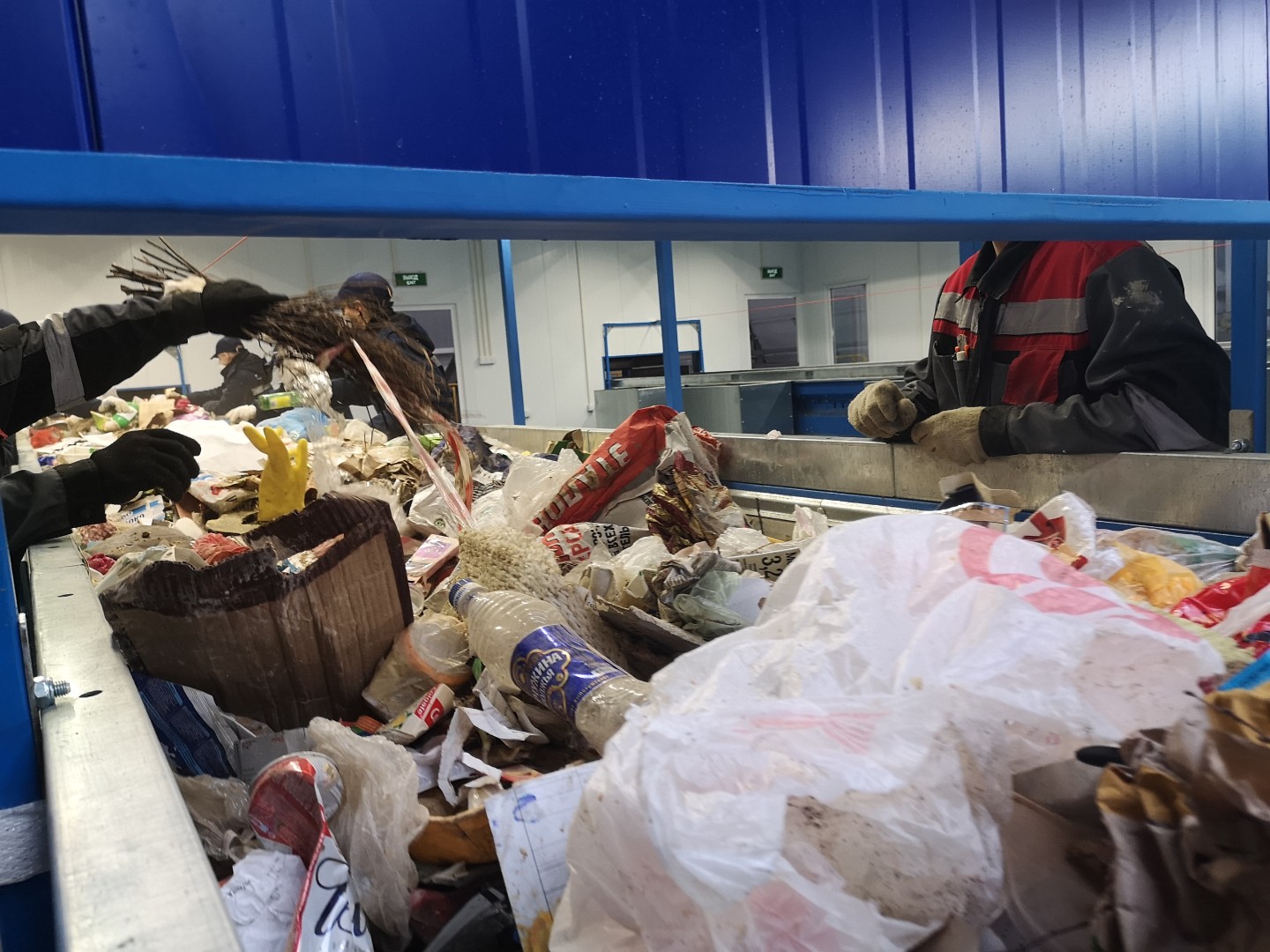
Перерабатывать по особой технологии смогут органику в уникальном цеху компостирования.
Разгружают машины в крытом бункере - отдельно складывают сухие отходы, отдельно смешанные.
После этого содержимое синих контейнеров попадает на специальную ленту, где начинается ручная выборка крупных фракций, стекла и осколков, тканевой ветоши, деревянных изделий и больших кусков прозрачного мягкого пластика.
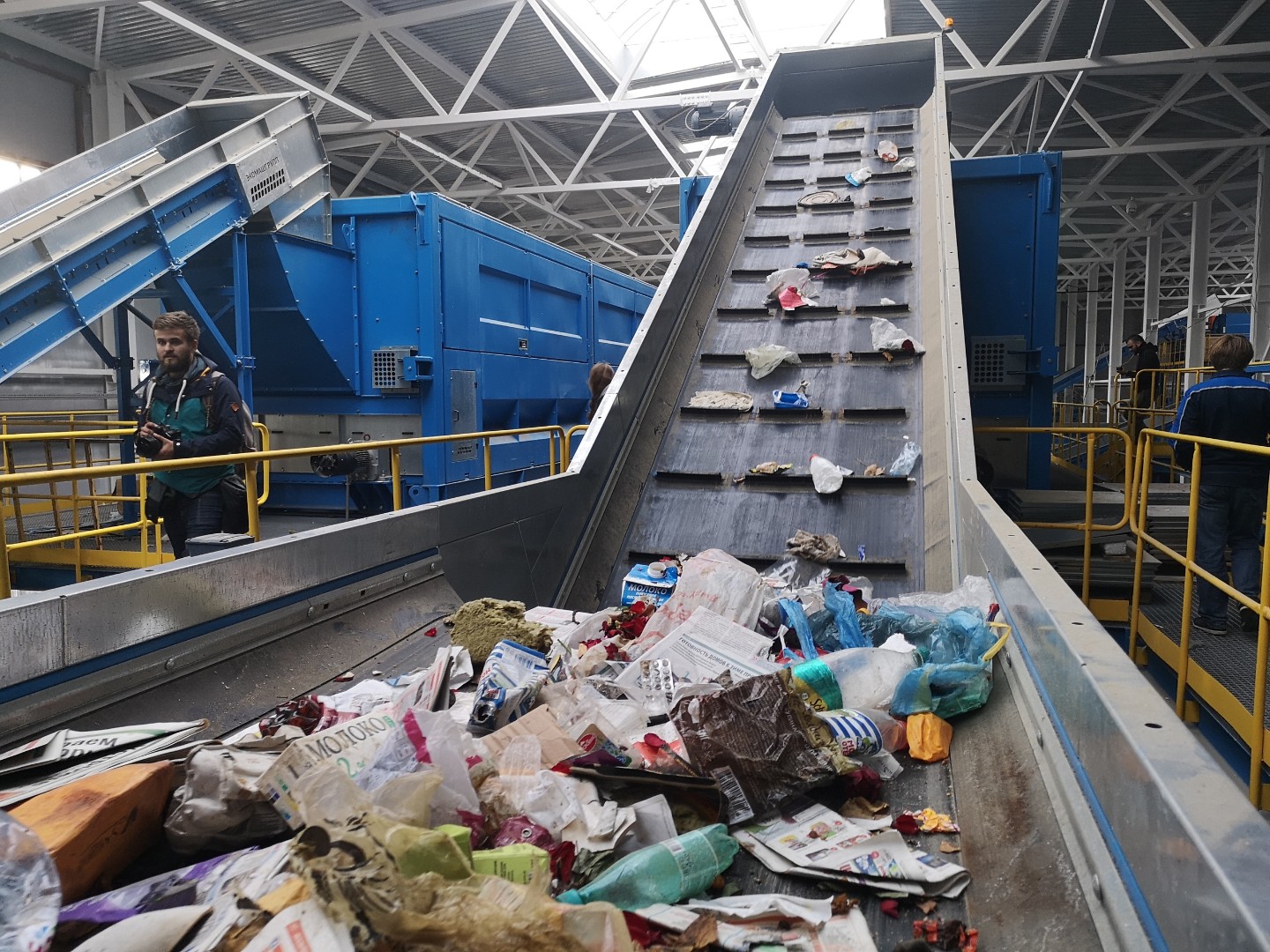
Стекло собирается в специальном бункере, крупные фракции из дерева поступают на дробление, а все, что непригодно к дальнейшему использованию, готовится к захоронению.
Затем начинается автоматическая сортировка. Отходы поступают на конвейеры и проходят через несколько этапов для выделения полезных фракций.
Сначала все потенциальное вторсырье проходит через «барабанный грохот» - трехфракционный барабан, где отходы делятся по размеру. Там же происходит отделение органической фазы, которая падает на отдельный конвейер и уводится в цех компостирования.
Смешанное сырье из серых баков проходит ту же процедуру: пакеты разрываются, отходы досортировывают вручную - убирают то, что не может быть компостировано. Затем в работу вступает барабан: органика и мелкий мусор, сильно загрязненный пищей, поступает в цех компостирования, а остатки пойдут на захоронение.
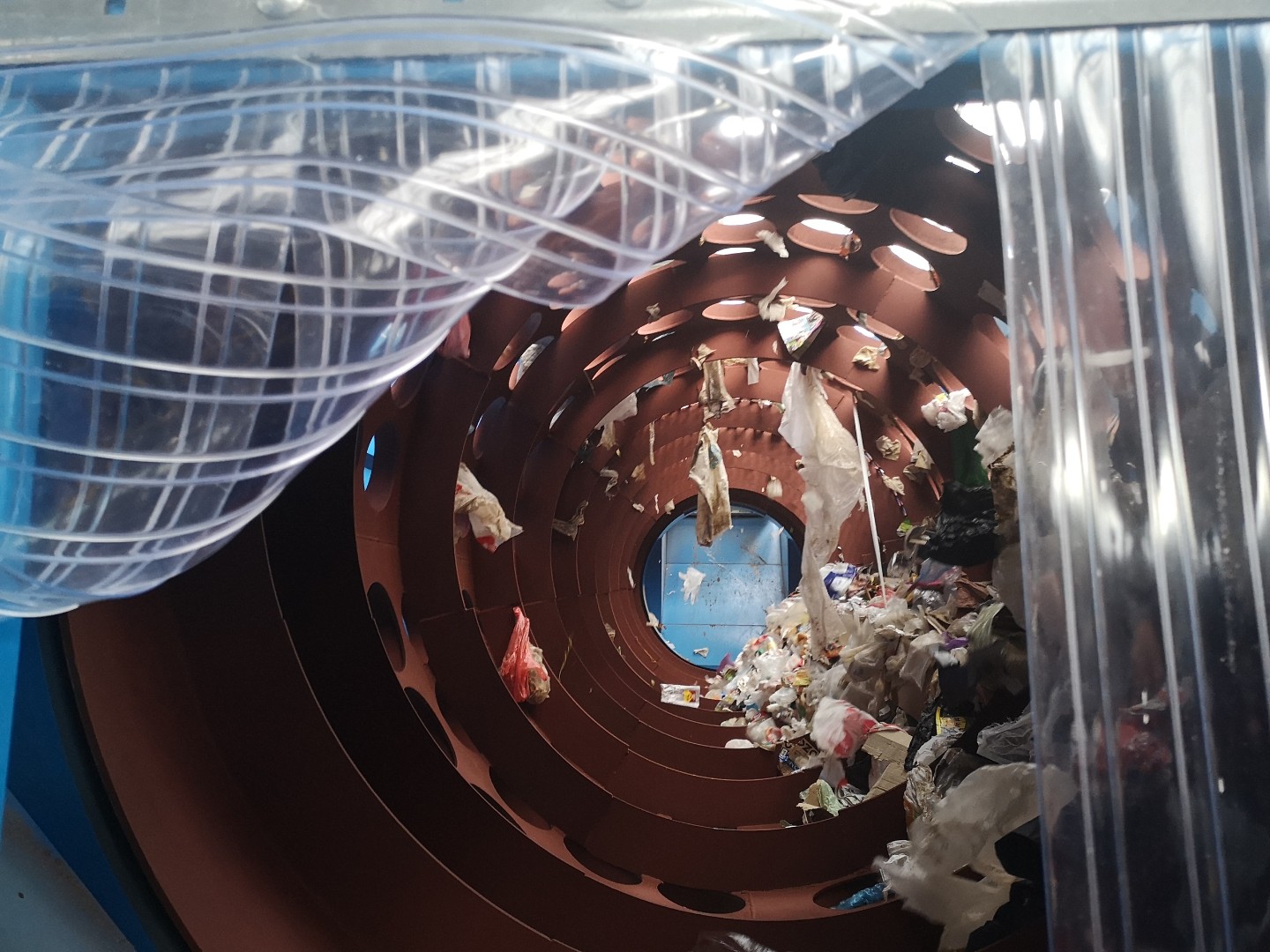
После барабана «сухие» отходы покрупнее и помельче идут по своим конвейерным лентам в оптические сепараторы, где мощным потоком воздуха «выдувают» бумагу и пластик. Металл поступает в магнитный сепаратор, где его разделяют на жесть и алюминий.
У пластика свой особенный путь. После отделения от бумаги и металла он попадает в баллистический сепаратор, где идет сортировка на 2D (пленка, мягкая упаковка) и 3D (бутылки, банки, контейнеры) полимеры.
Баллистический сепаратор представляет собой подвижные ступени и вентилятор: ступени подбрасывают отходы, а поток воздуха их обдувает. Плоское поднимается наверх и собирается отдельно, объемное - падает вниз и идет по другому конвейеру в следующий оптический сепаратор. На этом же этапе происходит дополнительный отсев неполимерных фракций.
«В оптических сепараторах заложено 60 алгоритмов работы под разные виды пластиков и других фракций. Можно выбрать один режим, который позволит наиболее качественно отделять определенный тип полимера. Мы настроили оптический сепаратор на PET-бутылку», - рассказывает главный технолог ООО МПК «Коломенский» Игорь Корнеев. “У каждого материала есть свои оптические данные, которые занесены в базу алгоритмов сепаратора. Луч попадает на идущие по конвейеру отходы и, если видит совпадение с настройкой, подает сигнал на пневмодатчик и «отстреливает» нужную фракцию на отдельную ленту, в нашем случае «улетают» бутылки».
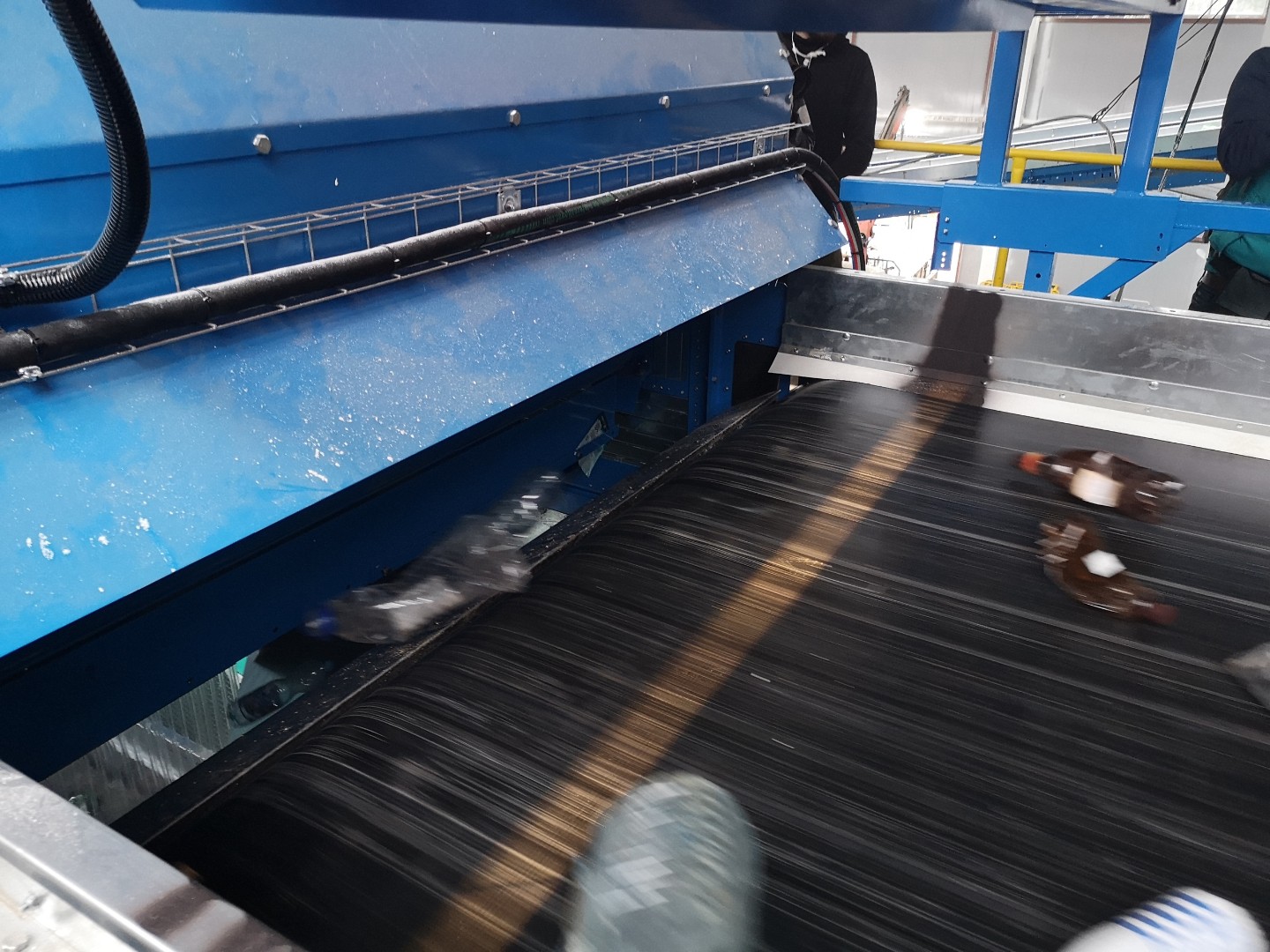
Остальные полимеры идут по другому конвейеру и снова приходят на ручную сортировку к людям, которые разделят их по разным типам. По словам главного технолога, PET-бутылок, по сравнению с другими видами пластика, поступает больше всего, поэтому сепаратор настроен на ее выделение, чтобы к людям на сортировку поступал меньший объем сырья.
«Конвейер достаточно мобилен и многофункционален. В зависимости от загруженности линии и соотношения отходов в исходном объеме ТБО (твердых бытовых отходах) его можно перенастраивать и выделять автоматически наиболее предпочтительный вид пластика» - поясняет Корнеев.
Затем вторсырье поступает на пресс. Каждая фракция концентрируется на своих конвейерных лентах и дожидается накопления необходимого для прессования объема. В одном брикете, в зависимости от прессуемого материала, находится от 200 кг до 1 тонны вторичного сырья. Кипы автоматически обвязываются проволокой и вывозятся на склад, где будут ждать, когда их заберет переработчик.
В среднем из поступающих ТКО планируют извлекать до 20% материалов для вторичного использования (стекло, бумага, картон, металл, PET и другие полимеры) и около 35% отходов пригодных для компостирования. Остальные 45%, которые не поддаются переработке, временно будут захоранивать по специальной технологии.
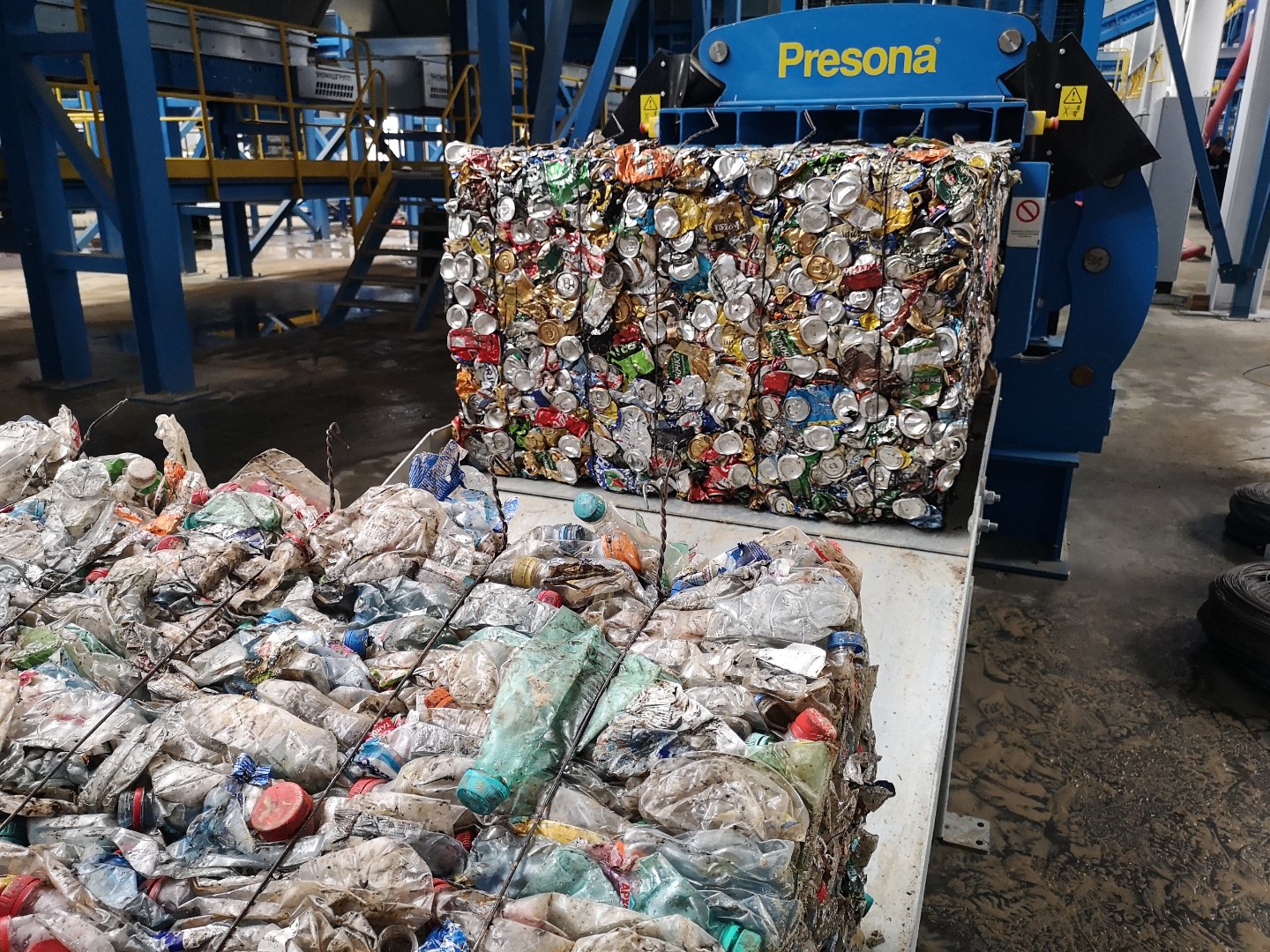
Перспектива для «хвостов»
Площадка для размещения непригодного к переработке мусора будет отличаться от обычного полигона и станет безопасным для окружающей среды местом складирования таких «хвостов».
На ней установят противофильтрационный экран состоящий из: бентонитового мата, уложенного на уплотненное земляное основание, геомембраны, не позволяющей фильтрату проникать в почву и грунтовые воды, и геотекстиля, который сверху будет засыпан защитным слоем грунта и песком с дренажной системой.
Фильтрат (осадки смешанные с гниющим мусором), образующийся на площадке захоронения, через систему дренажа будет поступать в очистные сооружения. Для очистки будет использоваться механическая фильтрация, нейтрализация и обратный осмос. Это позволит довести качество очищенных стоков до требований, предъявляемых рыбохозяйственным водоемам.
Однако помимо подобных КПО компания «РТ-Инвест» строит современные заводы по термической переработке отходов в энергию. После того, как эти заводы начнут функционировать, все непригодные для переработки фракции станут «топливом» для этих предприятий и превратятся в электроэнергию.
Новые заводы обещают предотвратить выбросы диоксинов, а шлак и летучую золу планируют использовать при строительстве дорог. Четыре таких предприятия должны построить в Московской области в ближайшие годы.
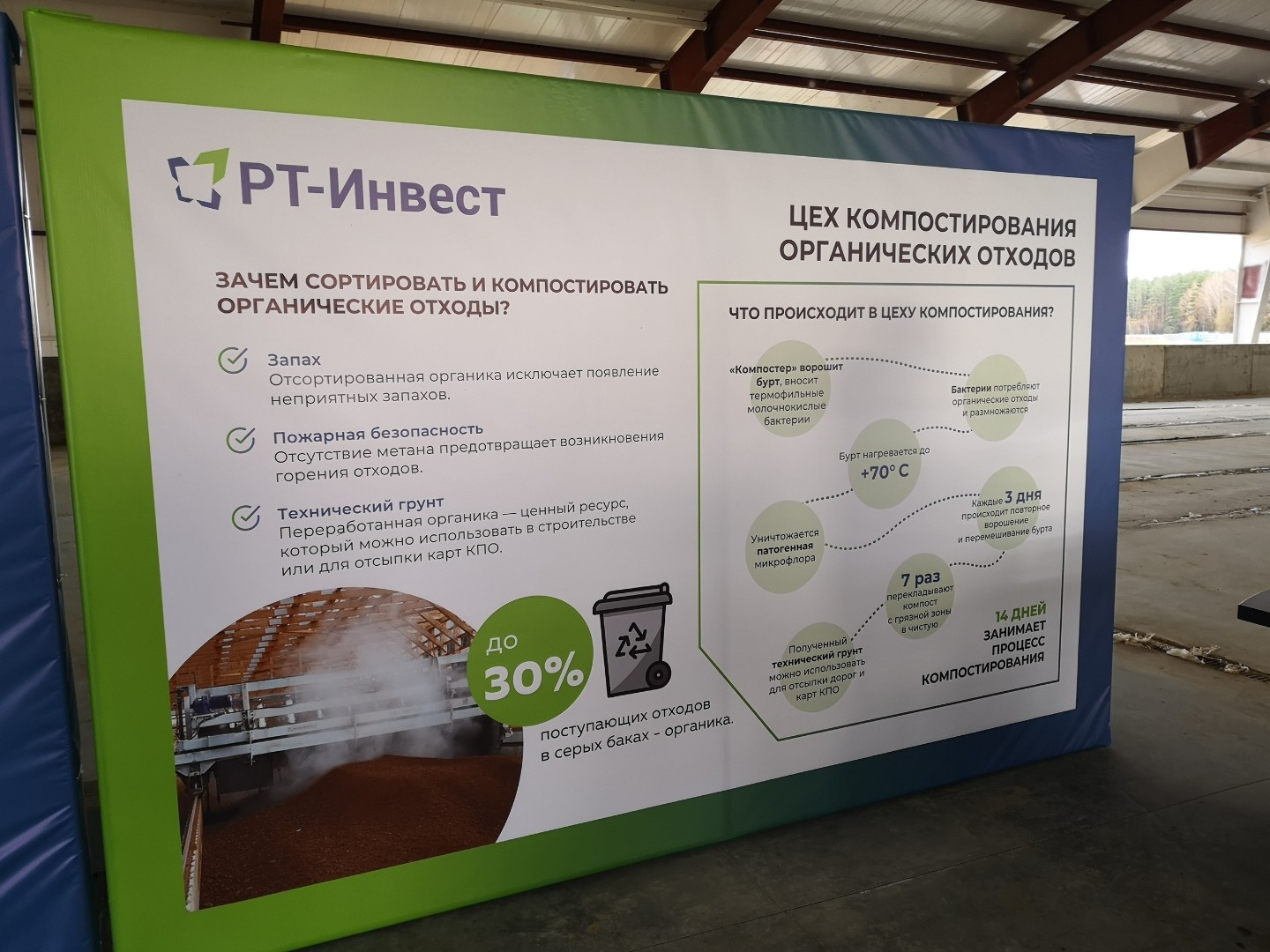
Органику - в компост
В течение месяца на Коломенском КПО должен быть окончательно возведен цех для компостирования органических отходов.
Все пищевые и растительные остатки, мелкая загрязненная бумага и прочие небольшие фракции, отобранные в барабане, отправятся на участок компостирования.
Цех будет представлять из себя закрытое помещение, в котором органику автоматически уложат буртами в 5-6 рядов. Размер бурта составит 100х3 метра, а объем - 500 м3. Каждые два дня полупродукт будут ворошить и впрыскивать термофильные бактерии штамма Pediococcus pentosaceus, которые ускоряют процесс гниения.
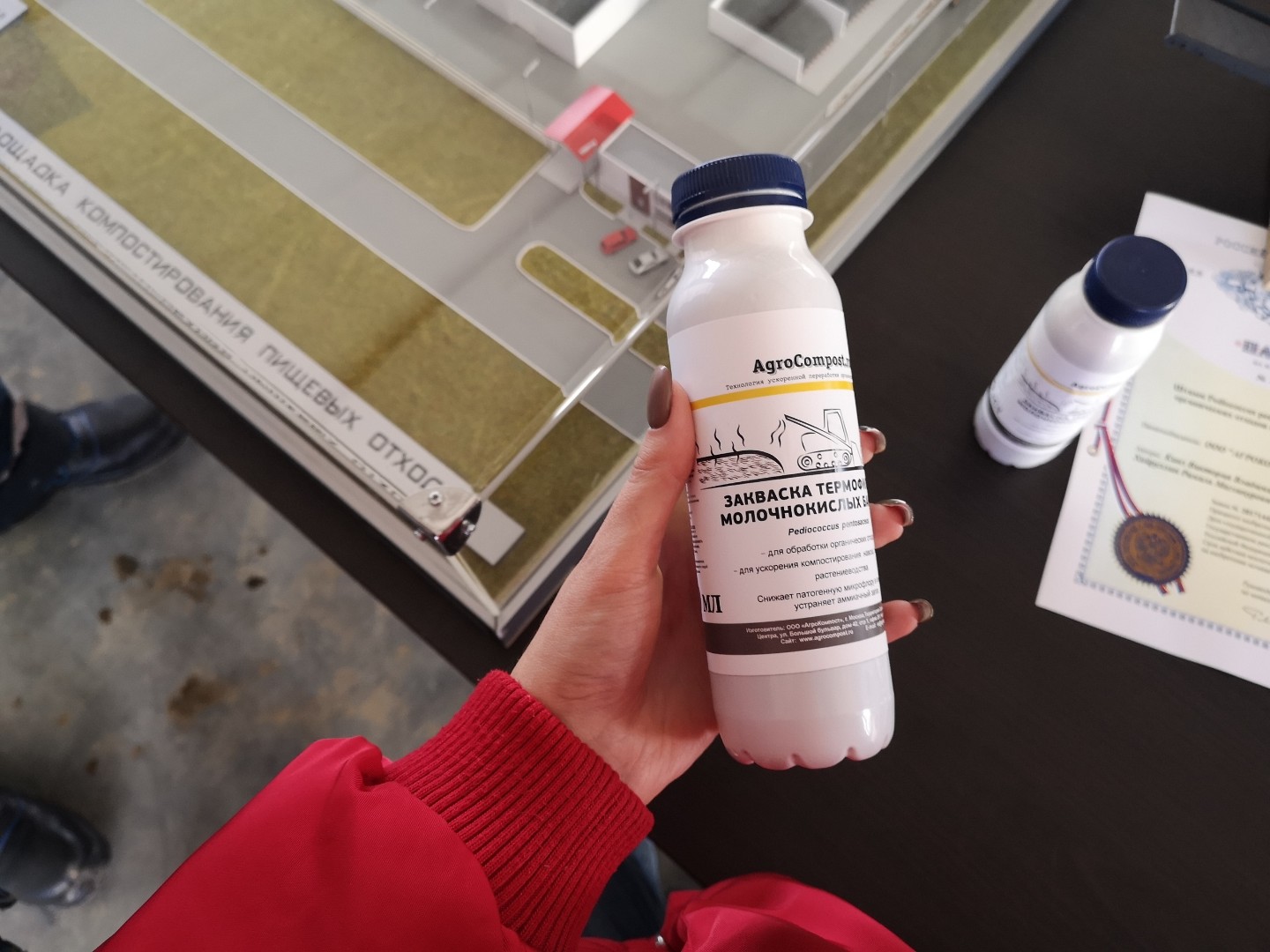
Эта специальная разработка компании «Агрокомпост» (резидент Сколково) позволит сократить срок разложения органической фракции до двух недель.
Для сравнения: аналогичный процесс в естественных условиях нашего климата занимает не меньше 2-3 месяцев. Средняя температура компостирования составляет 65-70 градусов - это позволяет уничтожить патогенную микрофлору и личинки насекомых.
Газообразные продукты гниения, такие как аммиак, углекислый газ, метан и соединения серы, не будут выбрасываться в атмосферу, а пройдут очистку и обезвреживание с помощью системы биофильтров, расположенной внутри цеха.
«Сам фильтр представляет из себя грубо говоря коробку, в которой лежит древесная щепа, пропитанная уже другим штаммом бактерий»,- объясняет главный технолог. «Эти бактерии питаются парниковыми газами и на выходе мы получаем обеззараженный воздух. Загазованность в помещении будет только в период гниения. В моменты обслуживания компостных буртов мы будем очищать воздух, чтобы никто не отравился».
В процессе компостирования будут получать технический грунт, который в дальнейшем можно использовать для озеленения городских зон, отсыпки откосов дорог и рекультивации полигонов ТКО.
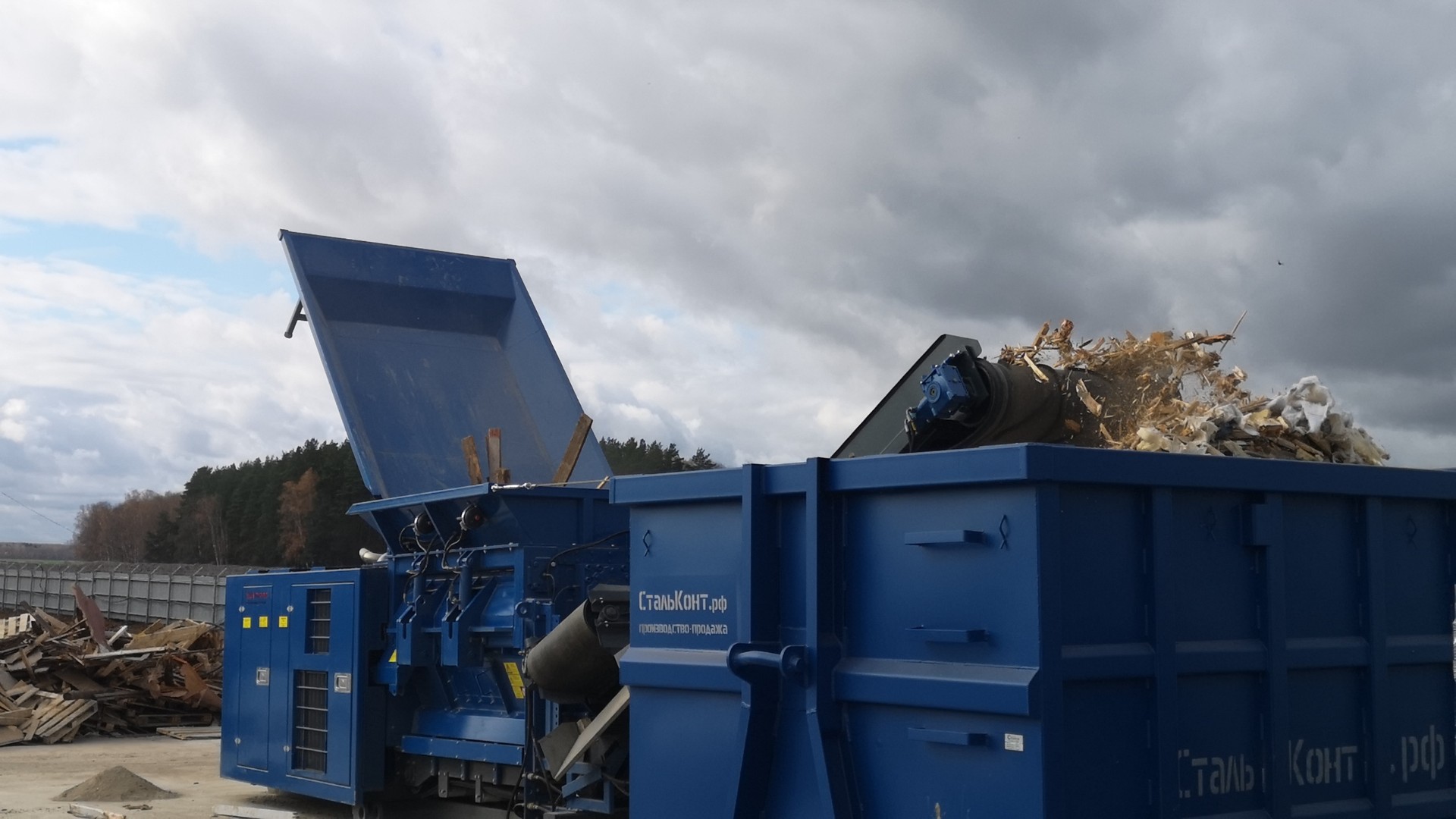
Крупногабаритные отходы
Крупные отходы, отобранные в приемном отделении цеха сортировки, направляют в бункер, а оттуда на площадку для измельчения.
Специальный шредер (дробильная установка) поставлен ведущим мировым производителем - немецкой компанией Husmann. Ее производительность составляет примерно 60 т/час, т.е. в сутки можно переработать более 1200 тонн крупногабаритных отходов.
КГМ (крупногабаритный мусор) собирают на контейнерных городских площадках и транспортируют до ближайшего пункта перегрузки. Чтобы не везти все на КПО и уменьшить логистические издержки, часть крупных отходов направляют на дробление прямо на этих пунктах. Шредер мобильный и позволяет перемещаться по разным точкам перегрузки и обработки отходов внутри кластера.
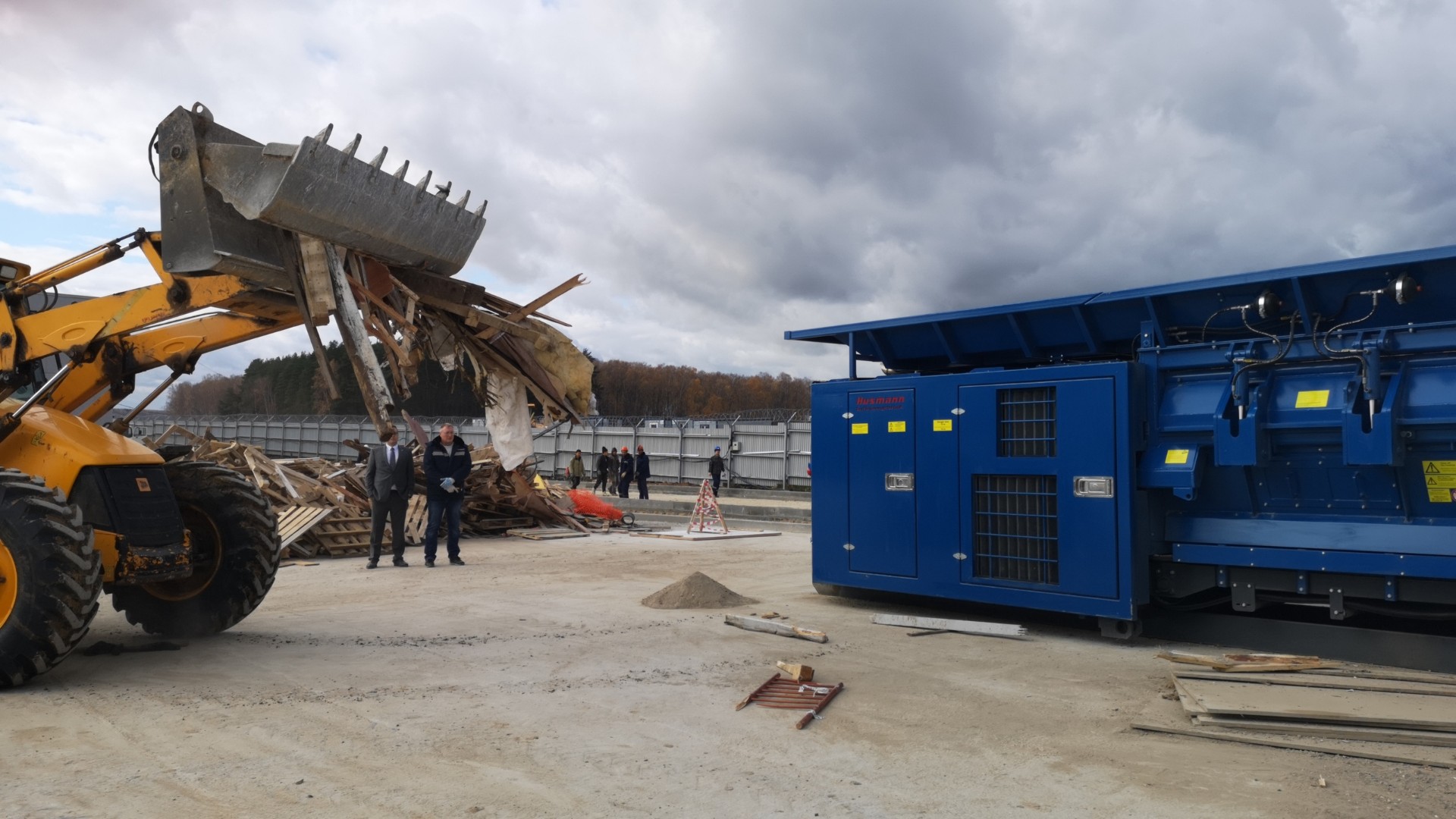
Под КГМ обычно понимают мебель, деревья, спил и порубочные остатки. Дробильная установка превращает их в щепу, которую в дальнейшем можно измельчить еще больше и использовать при засеивании газонов или для отмосток дорог.
«Сейчас такие фракции чаще всего захораниваются, хотя продукт переработки достаточно многофункционален», - рассказывает Дмитрий Петров, заместитель генерального директора УК «Региональный оператор» (входит в ГК «РТ-Инвест»).- «Если использовать такую установку на всех КПО, то мы сможем перерабатывать все крупногабаритные отходы в Московской области и уменьшить объем захораниваемых отходов еще на 15% только за счет дробления КГМ».
К крупногабаритным отходам также относят и технику, но на самом КПО, по словам Петрова, перерабатывать электронику пока физически не успевают, поэтому временно будут передавать ее сторонним предприятиям.
На вопрос об импортозамещении техники на КПО Дмитрий Владимирович честно ответил, что порядка 40% техники и автоматики на Коломенском комплексе были закуплены за рубежом. Однако более 60% технологий и механических узлов принадлежат отечественным разработчикам: от программного обеспечения на въездном контроле мусоровозов до целого цеха компостирования.
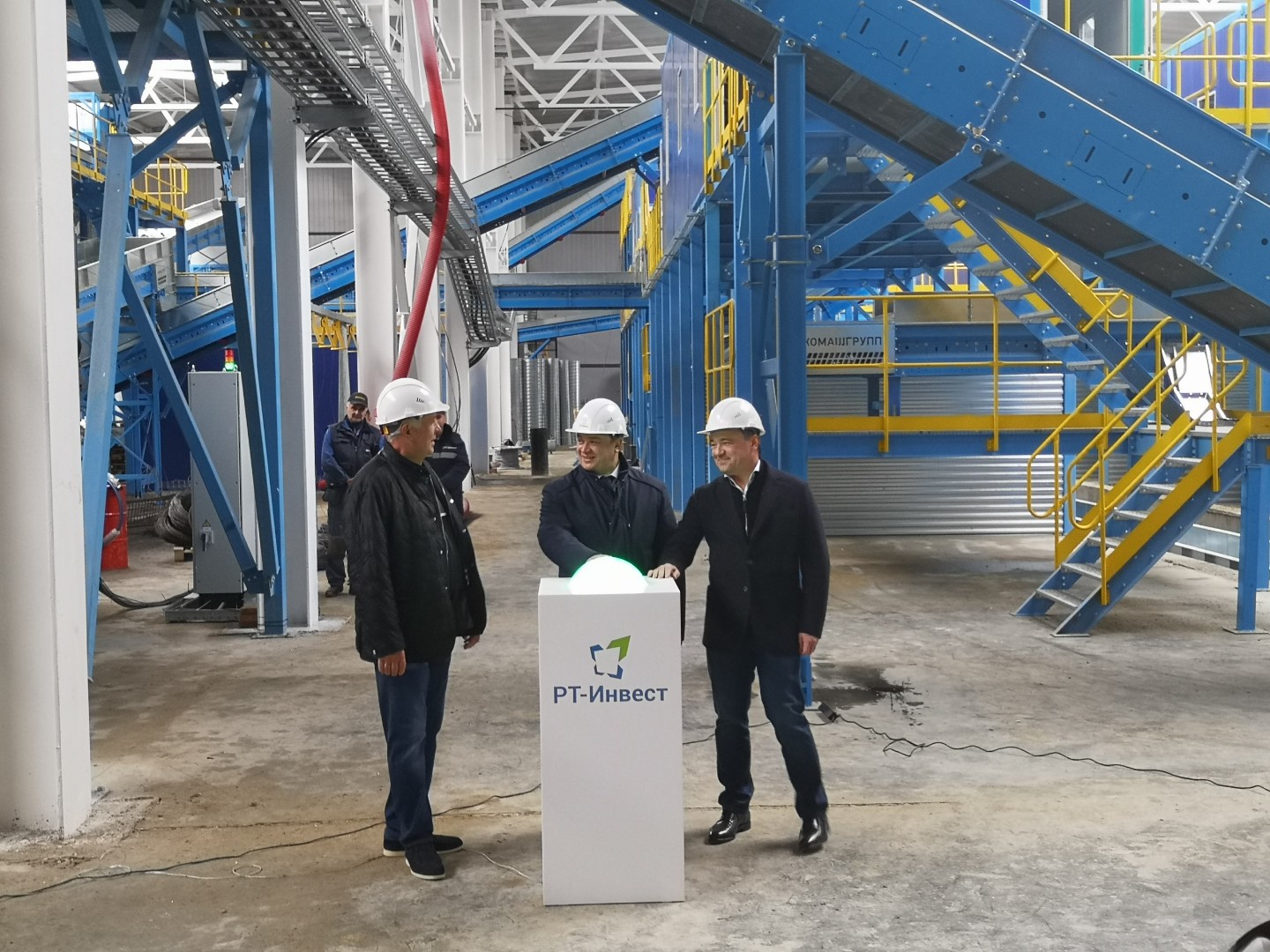
Новая система
Запуск первой сортировочной линии КПО проинспектировали губернатор Московской области Андрей Воробьев, глава госкорпорации «Ростех» Сергей Чемезов и генеральный директор «РТ-Инвест» Андрей Шипелов.
«В Подмосковье мы строим 12 таких современных комплексов, которые позволят закрыть все свалки. Жители больше не будут ощущать неприятных запахов, - сказал Андрей Воробьев. - Здесь используются самые современные технологии по переработке отходов, а компьютерные системы позволяют контролировать не просто каждый грамм, но и понимать морфологию мусора, прибывающего на КПО. Через месяц этот комплекс начнет работать в полную силу, что позволит закрыть полигон «Воловичи» в Коломне, о чем нас давно просили жители. Эффект от внедрения раздельного сбора отходов уже колоссальный. Даже в небольших населенных пунктах, несмотря на мнение скептиков, удается собрать большой объем пригодных для переработки фракций. Сейчас региональные операторы должны очень четко работать, открывать новые контейнерные площадки, запускать больше синих машин, потому что жители уже просят забирать “чистые” отходы чаще».
Андрей Шипелов заявил, что к 2022 году долю захоронения отходов в Московской области планируют сократить до 15%. «Этот комплекс соответствует всем европейским стандартам, а в чем-то даже их превосходит», - уверен Шипелов. «К концу 2022 года в Подмосковье будет полностью создана система, которая позволит минимизировать полигонные захоронения до 15%. Следующий шаг – это нулевое захоронение. Хотел бы отметить, что это возможно только благодаря слаженной работе и контролю первых лиц региона, госкорпорации и федерального правительства».
Три менее мощных комплекса уже успешно работают в Серебряных Прудах, Рошале и Зарайске. Еще три комплекса, подобных предприятию в Мячково, должны открыться в Сергиевом-Посаде, Кашире и Егорьевске. Остальные пять КПО будут возводиться в следующем году наряду с заводами по термической обработке отходов, которые станут частью новой инфраструктуры по обращению с коммунальными отходами в Подмосковье.
Анастасия Троянова